Automation system for food processor Niacet Tiel
Alewijnse updated the automation system in order to comply with the legislations and regulations.
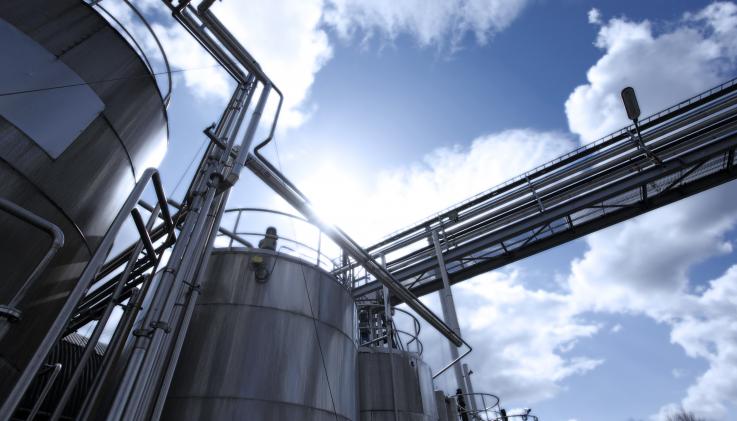
Our activities
Niacet Tiel needed to upgrade the outdated automation system of DP2 dry powder factory 2 in order to comply with the legislation and regulations and also keep the quality of its products at a constant level. The old ABB system was replaced with a Siemens S7 operating system. Now all the production components can be run by the same automation system, so the system is now standardised. To do this, we drew up a list of the customer’s wishes and needs and used them to write a User Requirement Specification.
Niacet is a leading producer of organic salts, including propionates and acetates, serving the Pharmaceutical, Food, Feed and Technical industries. With two longstanding and fully automated manufacturing sites, located in Niagara Falls, NY USA, and Tiel, The Netherlands, Niacet offers world-class quality products to a global market.
Validated automation system
In order to comply with FDA, the operation of the automation system must have been validated. We did this by applying Good Automated Manufacturing Practice (GAMP). With that validation, the system now complies with the FDA requirements. Alewijnse drew up a functional design for the new system, programmed PLC and SCADA, conducted a Factory Acceptance Test (FAT) and Site Acceptance Test (SAT) and, lastly, commissioned the new system.
Our implemented activities
- Replacing the ABB operating system in DP2 with the Siemens S7 operating system.
- Compiling a list of wishes and needs and a User Requirement Specification (URS). The customer determined the result of production, both quantitatively and qualitatively.
- The functional design was based on the generated URS, enabling us to create a system that produces the result desired by the customer.
- The automation system was validated with GAMP. This procedure was strictly followed and led to the structured development, programming, implementation and commissioning of the automation system.
- Before the automation system was implemented, the Factory Acceptance Test (FAT) was conducted with the customer. Together with the Niacet team, the software was tested down to the last detail. This meant that any differences in theoretical and practical interpretations of the URS were detected and adjusted immediately.
- After the verification process and the FAT, the PLC and SCADA were tested on location in the way described in the SAT protocol.
- The quality is now no longer largely dependent on the knowledge of service engineers, but is guaranteed by the technology/the system. Operators have been trained to work with the new system.
- The new automation system has run parallel to the existing system. During that time, it ran perfectly, which meant that the implementation/SAT could be successfully concluded.
Looking back at the procedure, I can only say I’m very satisfied. The careful observance of the GAMP method in cooperation with Alewijnse was a very transparent process that resulted in the validation of our automation systems, which now fully comply with the requirements of the FDA and therefore also the requirements of our customers.
Frans van Ettro, Supervisory Project Manager @Niacet
Indicators
Control: Siemens S7 317-2PN/DP PLC
Number of inlets and outlets: 400
Visuality: iFix SCADA
PC's: 1 server, 3 workstations
Ratio of hours: Design:Programming:Validating = 2:4:3